Control room & remote operation
Remote Control and use of an Onshore Operation Centre will give numerous benefits and will simplify the way to operate your plant. A human-centred design, taking all elements within PPTO (People, Processes, Technology and Organisation) into account, will ensure you get a "fit for purpose" Control Centre, tailored to your needs.
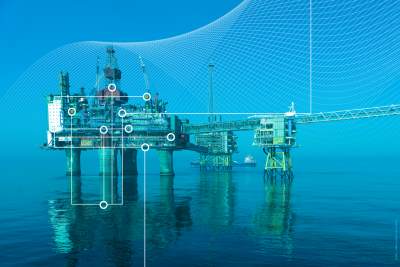
Remote control rooms and operation centres
Remote Access
To cater for new operational demands, companies need to allow outside connections to their networks. Companies may also require connection to networks outside of their own. This is especially relevant in light of the recent pandemic. By using traditional means of connection (VPN), there isn’t a good way of having insight into who gains remote access into networks and what actions are being performed, until it’s already too late. Even if most of the security measures have been taken care of on-site, computers located outside of the local network may be vulnerable to attacks. This opens the door for malicious users that may act as a known user to gain access to your systems. The number of data breaches has gone up exponentially since the first lockdowns were introduced, and this continues to be a major threat to integrity and security of information systems and the data stored on them.
As a BeyondTrust Partner, Eldor can provide solutions for safely accessing and keep control of active sessions towards remote assets. Locally deployed on the asset or delivered as "SaaS- Software as a Service". Industrial network reached through "jump clients" installed on clients and servers on the asset.
This software is based on two main pillars, each targeting different needs:
- Privileged Remote Access- allows employees, vendors, and contractors to access systems within your network.
- Remote Support- support your employees and clients wherever they are.
The importance of keeping track of your installed base is getting increasingly important as systems get more complex and the dependencies towards asset uptime and personnel safety get more linked towards the technology we use.
Eldor provides Cyber Security services to identify any vulnerabilities on your industrial networks and can help you bridge the gaps to comply with the government regulations, standards, and your own company guidelines.
Are you considering a new project?
-
The client may choose how we fit into their project model from adding capacity to taking on the full responsibility for delivery and approval from authorities.
-
For a greenfield project, we recommend to start with developing an operations and maintenance philosophy, and build on business cases.
-
For a brownfield project, a human factors and task analysis may be a good starting point.
Ivar Aasen onshore operations centre
Going from local to remote operation
How does local and remote operation compare?
What are the success factors?