There are many ways a plant’s process control system can be optimised, but regardless of the method used, as time goes by, the parameters that once worked so well might not be working anymore. This happens because of constant changes in the production facility, with some changes impacting the process’ ability to meet its objective. This creates a need for the process control systems parameters to be verified or updated on a regular basis.

What happens if we keep the system running as-is?
As many as 60% of the automated control loops among the plants worldwide are either underperforming or inefficient, because they are not well understood and handled by the operators (Thwaites, 2008). As mentioned in the previous blogs, running the process control system without a set of well-tuned parameters may work “just fine”, but the process is less profitable. Providing optimised parameters helps utilise the full potential of the plant and typically increases production throughput, production yield, lowers the energy consumption and need for maintenance in addition to ensuring a more consistent quality of the product.
How can we optimise the system?
There are many solutions for ensuring the process control system is performing at a near optimal level at all time, ranging from manual methods, without any use of software, to full scale performance monitoring software.
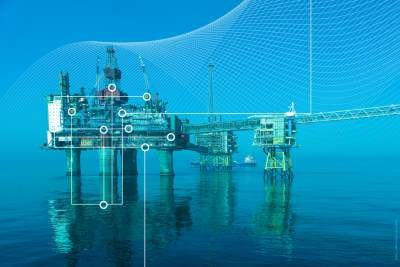
Manually optimising a process control system
Manual methods can be very efficient in finding good parameters and a lot can be achieved without using any kind of software tools, but some issues can still be difficult to detect. Most of the manual methods are also relying on step test data to obtain the necessary process information to provide the most accurate parameters.
Because of the economic potential in optimising a process plants performance, there has been developed a variety of software tools and simulators to assist with this issue.
Software monitoring services
Many software tools can provide a set of data if step-test-data is available. The most advanced software tools are installed on a server that is being fed live process data. From this data the software can monitor the control loop performance on a plant-wide basis and the best software can provide warnings of mechanical, tuning, and interaction issues in advance, by using the live data from the process facility.
Some performance monitoring solutions are equipped with a targeted set of key performance metrics (KPIs) that are proven to deliver actionable insight. The KPI’s are used collectively to decipher trends in the process data that are connected with a variety of challenges, ranging from mechanical and PID controller tuning issues to complications with the facility’s process architecture. (Controlstation.com)
Process instrumentation is critical to maintaining safe, efficient production. Should the instrumentation fail, it being a valve, a motor, or a damper etc. there are process monitoring services on the market that are able to identify these issues before they impact.
While poorly tuned controller can have a large, negative, impact on the performance of the process plant, it might not always be easy to identify them. A good monitoring tool enables the user to assess the tuning parameters in each PID controller, and it also alert the user to the PID loops that are impacting the most.
Process performance monitoring software makes it easier for the user to understand the process dynamics and how the process control loops are affected by it. As most processes are constantly changing the monitoring tool will not only help identifying process loops affected by these changes, but also help understanding which changes affect the process and how.
How should I choose a software for my plant?
There are many factors on which to base this decision, including the size of your company, courses or training required to use the software, the time it takes before the solution is up and running, to name a few. You should also consider what type of support you need before making a decision on using a specific software, as this will often have an effect on the final price.
Should I use an integrating company to service the process monitoring software?
An operating company can purchase the software monitoring tool and utilise the software itself, without using any third-party services. But, the software requires time, resources, and training in order to utilise the full potential of the software and it is in software providers’ experience that operators too often end up with leaving the responsibility for maintaining the software, interpreting the data, and create reports to one employee who either doesn’t have the required time available to do it or leaving it to one employee who later on gets assigned to a new task, leaving the software without a responsible person.
In short; using an integrating company ensures the full potential of the software is utilised, returning maximum result on the investment.