The objectives of an automatic control system are to regulate the process to meet the final product specifications and minimise waste production and energy consumption, hence lowering the environmental impact of the process and maximising the production rate, while ensuring safe operation. Because operating as close as possible to these maximum or minimum objectives are most profitable.
How do you know if your plant is performing at an optimal level?
These key production objectives must be satisfied even when the process is subjected to disturbances during operation. Disturbances can be variations in feed composition, variations in ambient temperature, sensor noise, equipment fouling, and more
Unless you have taken measures to ensure that parameters going into the process control system have been carefully selected through a systematic approach, taking process dynamics into account, the answer to this question is likely to be "no."
A non-optimised plant is not always easy to recognize as the plant may be working “just fine.” Typical indicators of a non-optimised process control system are controllers operated in manual, large oscillations in the process, and that the operators are experiencing difficulties controlling the plant, but even without these indicators, it is a general rule that when it comes to automatic process control, there is almost always room for improvement!
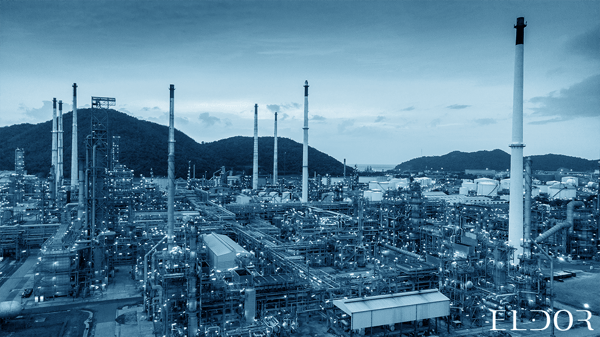
Why is it important to have an optimised control system?
In a visit to any random process plant today, we are likely to find that as much as 85% of the controllers are performing ineffectively when operated in automatic mode, meaning there is a lot of untapped potential when it comes to the performance of the controllers. In addition, 30% of PID loops are operated in manual mode (Chicago process solutions summit, 2020). These numbers are showing that Process Control regulation is a field of expertise that is often neglected. The good thing is that it is not too late to do something about the control system's performance after the process plant has started production.
Optimising the plant's performance with regards to the process control system is likely to decrease the energy consumption by 5-15% and decrease the defects occurring in the production plant with as much as 25-50% (Chicago process solutions summit, 2020). Improving the tuning of existing controllers will increase the productivity and improve the product quality for any plant (Cybernetica, 2020).
Example of from a paper production factory
If a produced product fails to meet the specifications set by the customer, the final product could end up being sold for a significantly reduced price resulting in a negative economic impact on the process plant. Meeting the product specifications is, therefore, of the utmost importance.
Suppose we are refining a product or making a paper sheet; Refining the product to a purity level higher than the minimum specification set by the customer means we are using more energy than required. Or in other words, if a product is sold with an impurity and the customer has set a maximum acceptable limit for the contaminant, it requires more energy to remove more contaminants than required. When producing the paper sheet, it requires feedstock to produce a paper sheet. It so follows that producing a thicker sheet than the customer will accept on delivery is ultimately wasting feedstock. By operating the process as close to the permitted thickness constraint, the use of feedstock is reduced to a minimum, and the processing facility is more profitable.
Whatever the operating constraints set for the process, approaching the targets will ultimately translate into operating each process unit as close as possible to the desired setpoint value for the different process variables, such as temperature, pressure, flow, concentration, etc. If the process is poorly controlled, the measured variables can exhibit large variability over time. Figure 1 is an example of a poorly controlled process, where the measured process variable is varying a lot, and consequently, the setpoint has to be set further away from the operating constraint to ensure the process variable stays within the operating constraint.
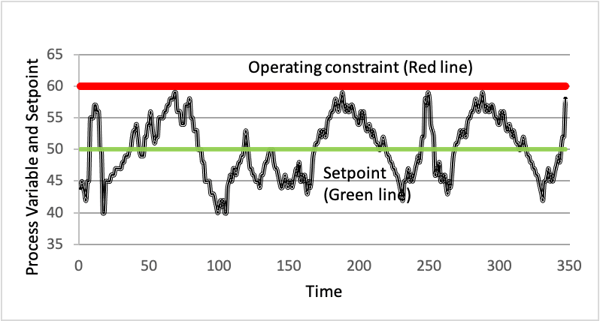
In figure 2, we see the same process with improved control. The variability in the process variable is reduced significantly, and as a result, the setpoint can be moved closer to the constraint.
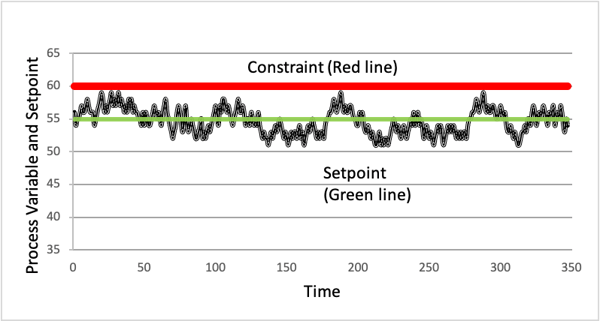
The result of moving the setpoint closer to the constraint is an increase in profitability in the process.
Further recommendations for minimising control system problems
By minimising the variations of the process variable, the set point can be moved closer to the constraint. Operating the process closer to the constraint increases the production throughput and the quality of the product and makes it the quality more consistent. It also lowers the consumption of energy and feedstock. To operate as close as possible to the constraint, the Process Control System needs a set of well-tuned parameters on a continues basis as most processes are constantly changing.